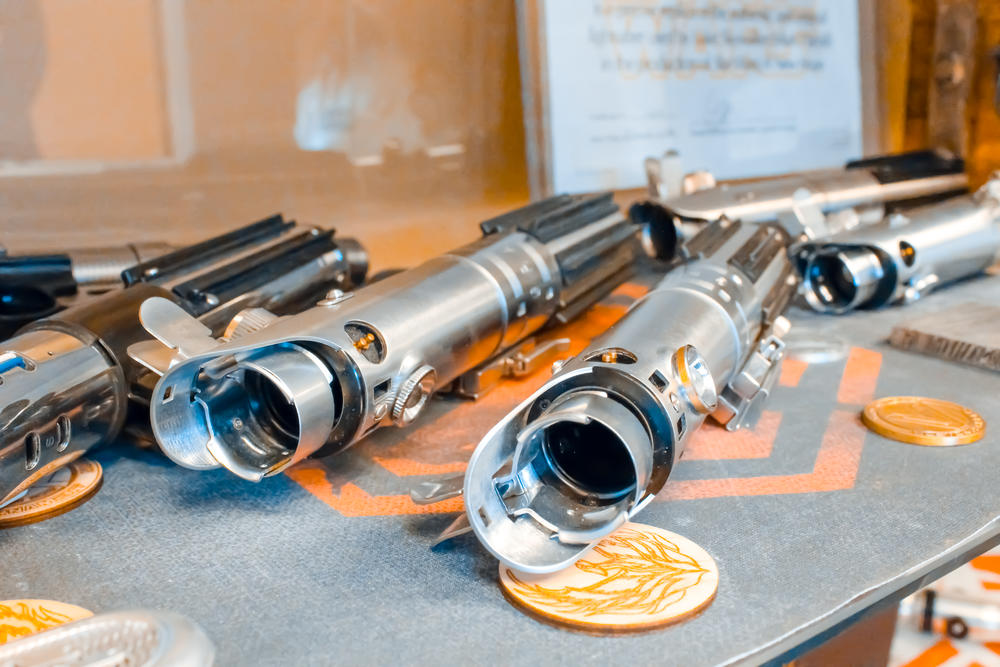
Section Branding
Header Content
Georgia Business Strives To Make Best Lightsaber In Galaxy
Primary Content
Not so far, far away, in an unassuming warehouse in Cumming, local Georgia business Vader's Vault has gone to extraordinary measures to create some of the best replica lightsabers — the laser sword weapon made popular by the Star Wars franchise — in the galaxy.
Its work is a far cry from the plastic versions typically seen for sale at a toy store. The models on its website can range from several hundred to thousands of dollars and boast names such as "Dark Enforcer" and "Sovereign Elite."
Popular YouTube channel "Star Wars in Real Life" recently ranked Vader's Vault as one of the top vendors in the world to buy a lightsaber.
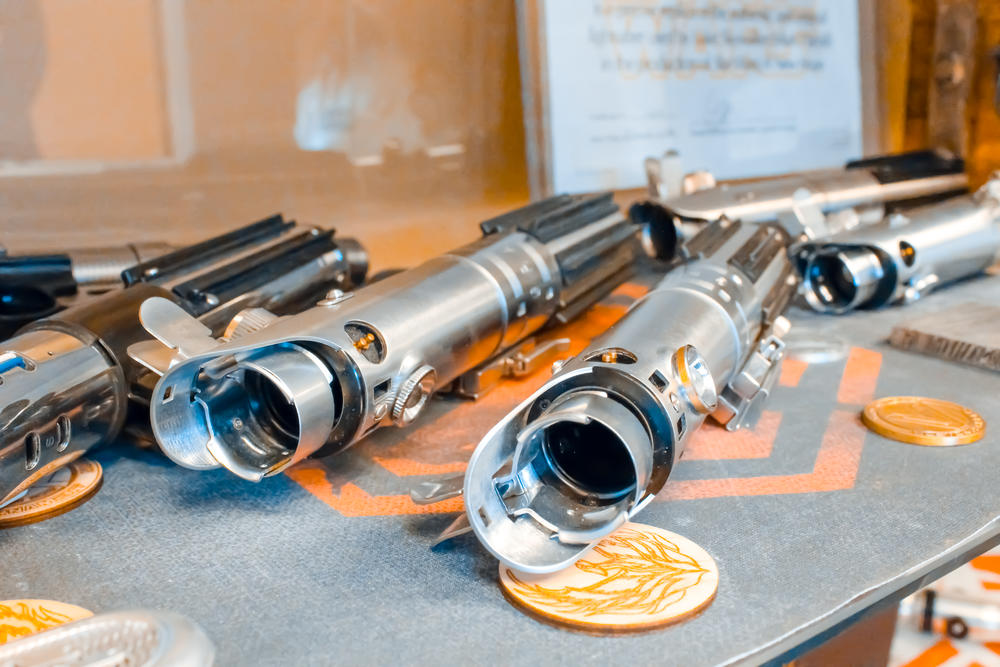
Walking through the Vader's Vault workshop, first glances wouldn't suggest that it was unlike any other local business. But looking a bit closer at the various workstations full of futuristic sword hilts and circuitry, the numerous employees wearing Star Wars tees, the stacks of blueprints of saber designs — and, of course, the gilded display cases housing an array of different iterations of the science-fiction weapon — it becomes clear that something Force-like is at work.
A step into a larger world
Owners Deana and Alan Johnson didn't originally set out to create lightsabers for a living. The couple met while working as managers at Radio Shack in Orlando until the struggling retail chain started making cutbacks and changing policies. They then went into ventures like real estate and landscaping. Through it all, Star Wars was a common bond for them both.
Deana recalled the feeling of seeing Star Wars Episode IV: A New Hope, the first film in the saga (then titled simply Star Wars), in theaters in 1977.
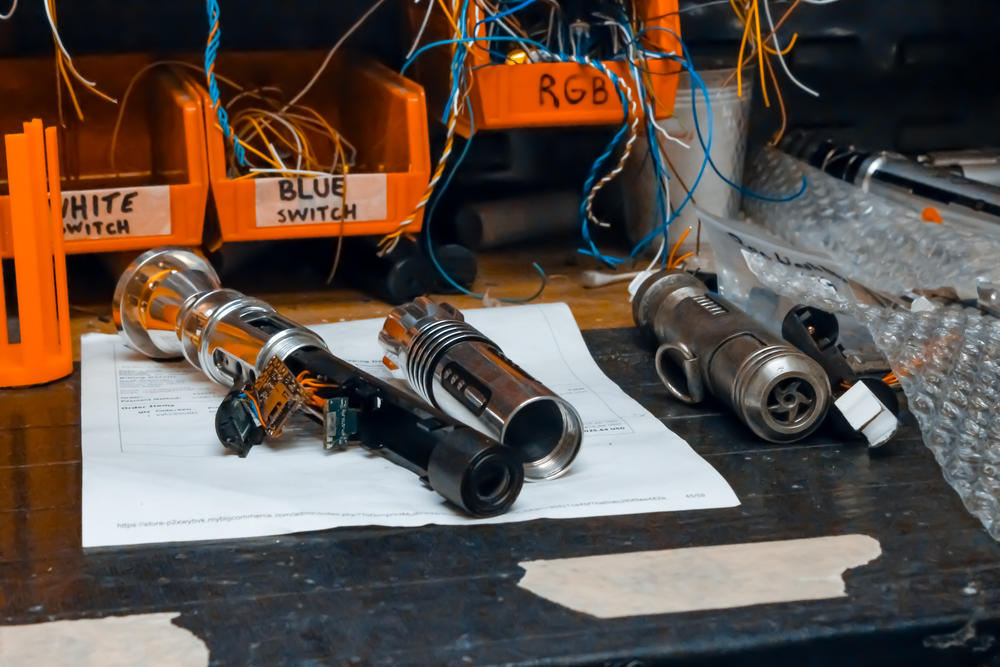
"Nobody really knew what to expect," she said. "You went in this theater, you saw this thing, and it was mind-blowing because to be there at that time, there was nothing else like it."
Alan had similar recollections.
"I think it was that marriage of the cinematography, the technology, the special effects and a story that people relate to," he said. "And it was just the perfect time for it."
Their venture into "sabercrafting," as the community built around creating replicas of the weapon calls it, began when Alan and their son both broke their leg at the same time.
"During that time was when we started to actually physically play with the sabers as therapy for them while their legs were broken," Deana said.
It was then the Johnsons found themselves connecting with others around the world who also loved making recreations of the weapon. When they decided to sell one of their handmade creations on online auction site eBay, they realized they were onto something big — after an intense bidding war, their lightsaber sold for thousands of dollars.
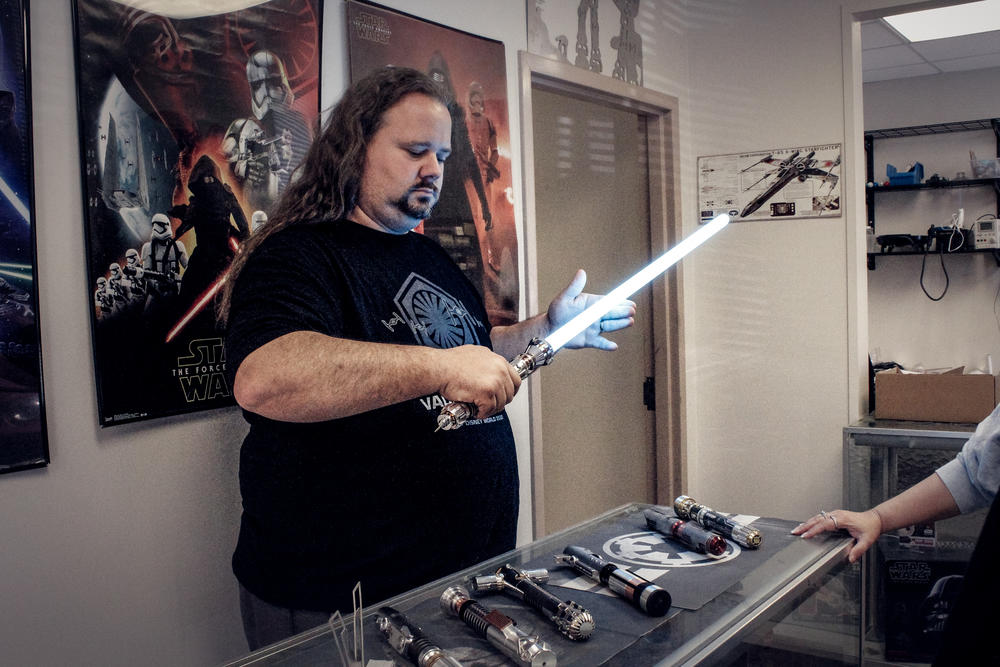
"We put one on there and it was the highest that one had ever sold on eBay," Deana said. "It was our first real custom. And some of the people that were in the bidding war contacted us for commissions. So, all of a sudden we went from, 'Hey, we're just going to try making one!' to having a whole business because now we've got orders."
So, not long after the December 2015 release of Star Wars Episode VII: The Force Awakens, Vader's Vault was born.
I see you have constructed a new lightsaber
Those first models were made from PVC material. Eventually, the Johnsons strived to perfect their model even further and switched to crafting with metal.
The only problem was the lightsaber still didn't make its iconic buzzing sound when it was lit — a problem they set out to fix.
The struggle at the time was that no soundboard chips could fit inside a realistically sized lightsaber hilt. Their solution? They commissioned a custom one to be made, reaching out to a fellow lightsaber hobbyist they had met who lived in France.
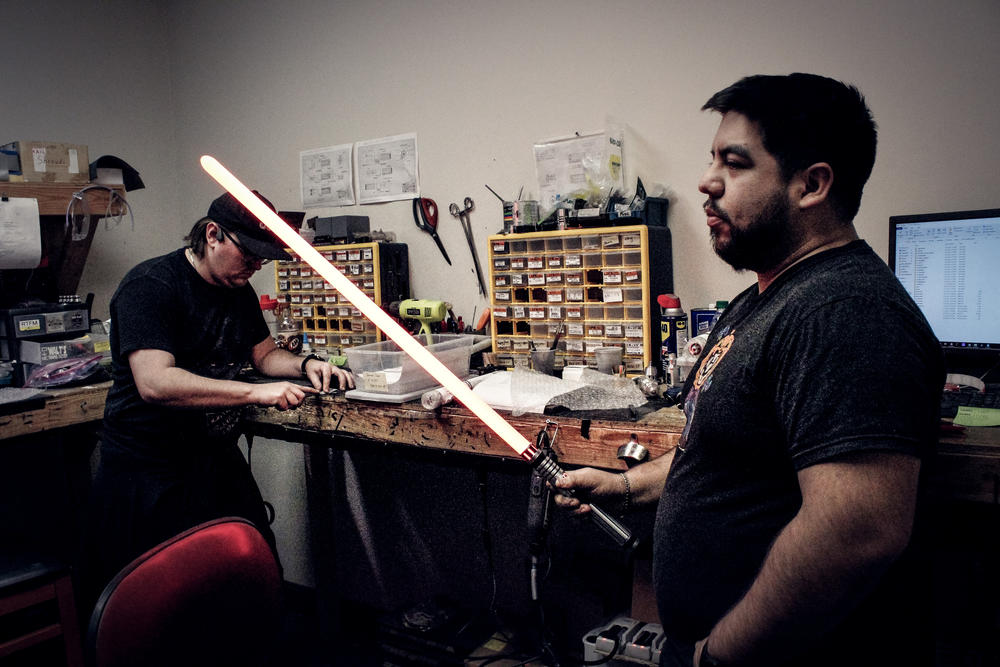
"So we had a conversation," Deana said. "I said, 'Look, I know you make soundboards, but your soundboards are too big, We need something about this size.' We gave them all of our specifications, everything."
Alan said their motivation for taking steps to perfect their product is a desire to seize upon childhood memories.
"We all wanted the toys we couldn't have as kids," he said.
Deana said it's about making the fantasy of a lightsaber as real as possible.
"The experience now and what we can provide is so close to what's in the movie, other than having a real plasma blade coming out," Deana said. "Other than that, it's so close that it is a really emotional experience when — when somebody who can go back to being six or seven years old, mentally, for that moment."
"At least once a week, I have grown men crying on the phone," she added.
The Johnsons do not exaggerate when they talk about attention to detail.
During the tour through their workshop, a pair of employees could be seen hand-weathering lightsaber hilts, creating a rugged, worn effect on their surface. Deana is quick to point out that all their weathering is done with accurate attention to where spots on the hilt would actually be worn down after being gripped over years of combat. The idea came to her after looking at swords with similar aging. Customers can order the feature, along with other customizations, for an extra fee.
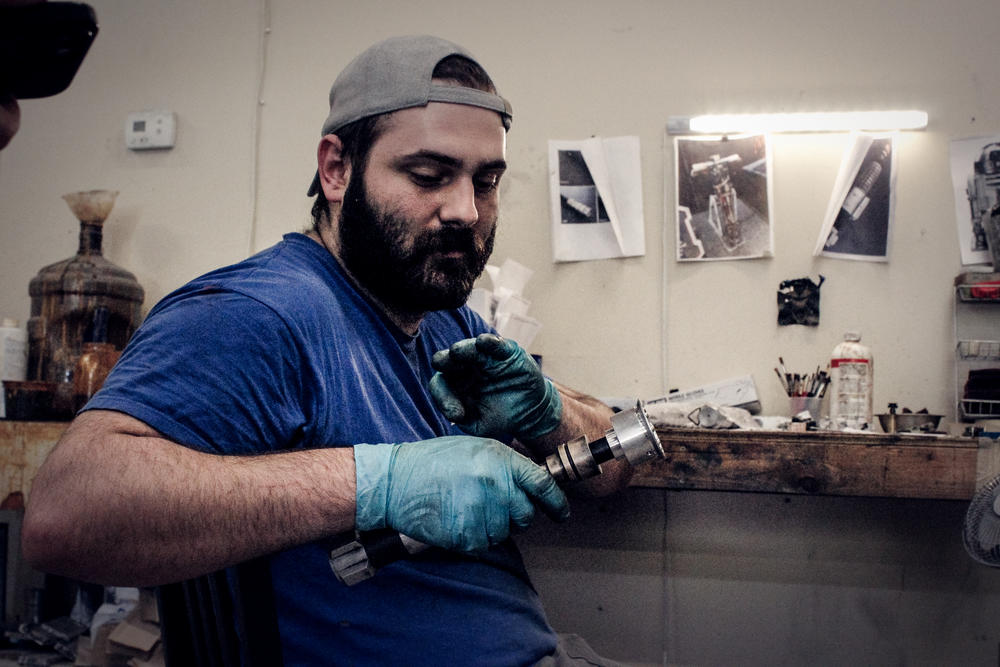
In another room, employees wire and test and perfect the saber's lighting effects. Alan takes a moment to show how the saber blade actually sparks and crackles when dragged along a surface, accurate to the films.
While some might call this level of detail excessive, it's clear that Vader's Vault has its loyalists. A huge whiteboard in the office lists a long line of pending orders, several denoted as custom-designed. The average turnaround times for a saber can be 26 to 32 weeks.
'A light' in dark times
Remarkably, Alan said that while other businesses have suffered during the pandemic, their orders have increased since it began.
"People are home with a lot of time on their hands and they're like, 'I need a light,'" he said.
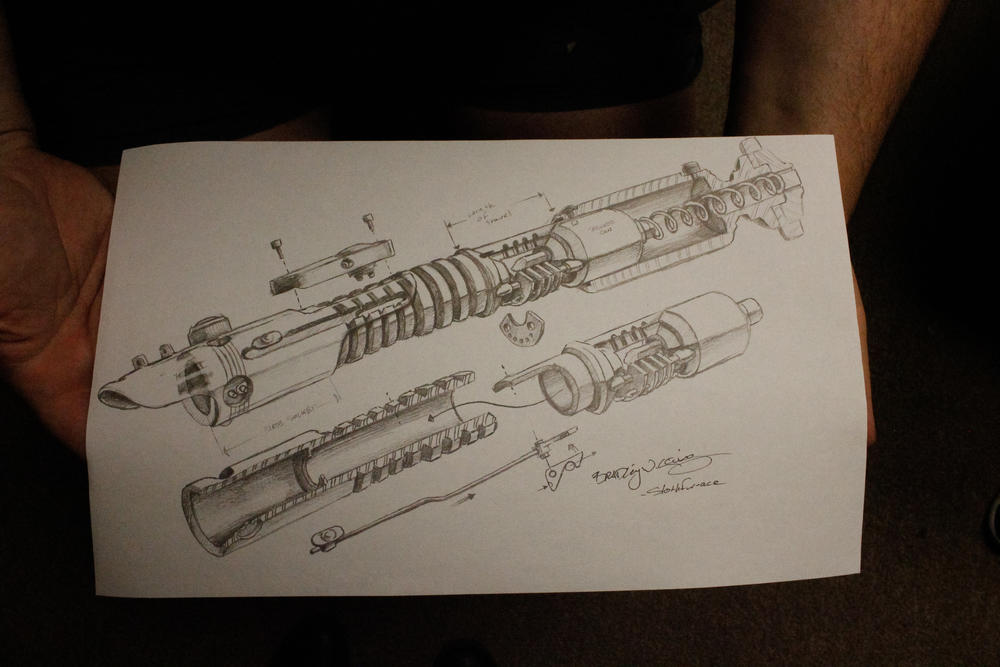
The Johnsons say they've received incredible tokens of appreciation since going into business.
"We get letters from people, from adults," Alan said. "We get letters from kids. We get people who send us baked goods."
Deana said one veteran was so moved by his lightsaber, he went an extra step.
"He sent us his flag and his personal challenge coin," she said.
And for some kids, their sabers have been a piece of fantasy in an otherwise trying time.
"We don't advertise it a lot, but we do a lot of charity: We're oftentimes working with terminally ill children, and that's difficult," Deana said, her voice wavering a little. "I remember one little boy about four or five years ago; he was buried with his saber."
"He loved it so much," Alan added. "And that for us, that's — that's why we do this."
When asked why Star Wars means so much to them, they both hesitated at what felt like a giant question.
"I mean, it is a community," Alan said. "Yeah."
"Star Wars is so huge and so varied and so global that you can find belonging and involvement at every stage," Deana said.
Walking through the warehouse full of sabers and hilts, it would be easy convince yourself that the small shop in Cumming was instead located in a rugged back alley of desert planet Tatooine, or deep in the trees of the forest moon of Endor. The shop does carry with it a sense of two fans who made their fantasy a reality, against the conventional odds.
"It was a massive leap of faith," Deana said, then smiled, taking a pause. "I guess we had the Force on our side."